What You’ll Learn In This Blog:
- Essential differences between the primary types of blow molding
- Advantages and applications of each blow molding process
- Tips for selecting the appropriate blow molding technique for your products
Blow molding is a widely used technique in the manufacturing of plastic, glass and products. This method involves inflating a hot, hollow plastic parison (a tube-like piece of plastic with a hole in one end) inside a closed mold, so the plastic shapes itself into the mold’s configuration.
From everyday household items to critical industrial components, blow molding offers a flexible and cost-effective solution for creating high-quality products. Here’s an overview of the primary types of blow molding used in the industry today:
1. Injection Blow Molding: This process begins with the creation of a preform, a basic shape of molten plastic that is first injection molded. The preform is then reheated, placed into a blow mold, and air is used to inflate it into its final shape.
Advantages: Injection blow molding is extremely precise, making it perfect for products requiring tight spec finishes like cosmetic bottles.
Applications: It is predominantly used for small to medium-sized bottles in the pharmaceutical, personal care, and food industries. Ideal for HDPE, LDPE and PP Resins with smaller size bottles and tighter neck tolerances.
2. Extrusion Blow Molding: Extrusion blow molding, the most common type of blow molding, extrudes a continuous parison that is then enclosed in a mold. Air is blown into the parison, inflating it to conform to the shape of the mold cavity.
Advantages: This method is highly versatile, allowing for the production of complex product shapes and sizes, including large items.
Applications: Ideal for any size container from pharma drug bottles. Cosmetics, automotive fuel tanks, industrial drums, and recreational equipment.Ideal for HDPE, LDPE and PP Resins.
3. Stretch Blow Molding: Stretch blow molding combines the steps of injection blow molding with a stretching stage, where the preform is mechanically stretched and then blown to enhance material properties.
Advantages: This process improves clarity, barrier properties, and strength, making it suitable for high-quality packaging solutions.
Applications: Commonly used for manufacturing water and soda bottles, or any container that needs to withstand internal pressure or enhance product shelf-life. Ideal for PET resins for smaller bottle sizes and tighter neck tolerances.
Selecting the Right Blow Molding Process
Choosing the appropriate blow molding process involves considering factors like the material, product specifications, production volume, and cost-efficiency. Recent innovations in blow molding technology focus on sustainability—reducing plastic waste, utilizing post-consumer recycled materials, and enhancing process efficiency. These advancements are vital as the industry shifts towards eco-friendly packaging solutions. Blow molding technologies are continually evolving, driving innovations in product packaging. By enhancing material properties and process efficiencies, manufacturers can meet the growing demand for durable, lightweight, and environmentally responsible packaging.
Stay Updated with the Latest in Packaging Solutions!
Keep ahead in the packaging industry by following our latest updates on social media (Linkedin, Instagram). Subscribe to our biweekly newsletter here for the newest insights and strategies directly in your inbox. Explore more detailed articles on our website here, and tune into our Product and Packaging Powerhouse™ Podcast, where we talk about industry trends and innovative solutions.
Connect with us today and enhance your packaging knowledge.
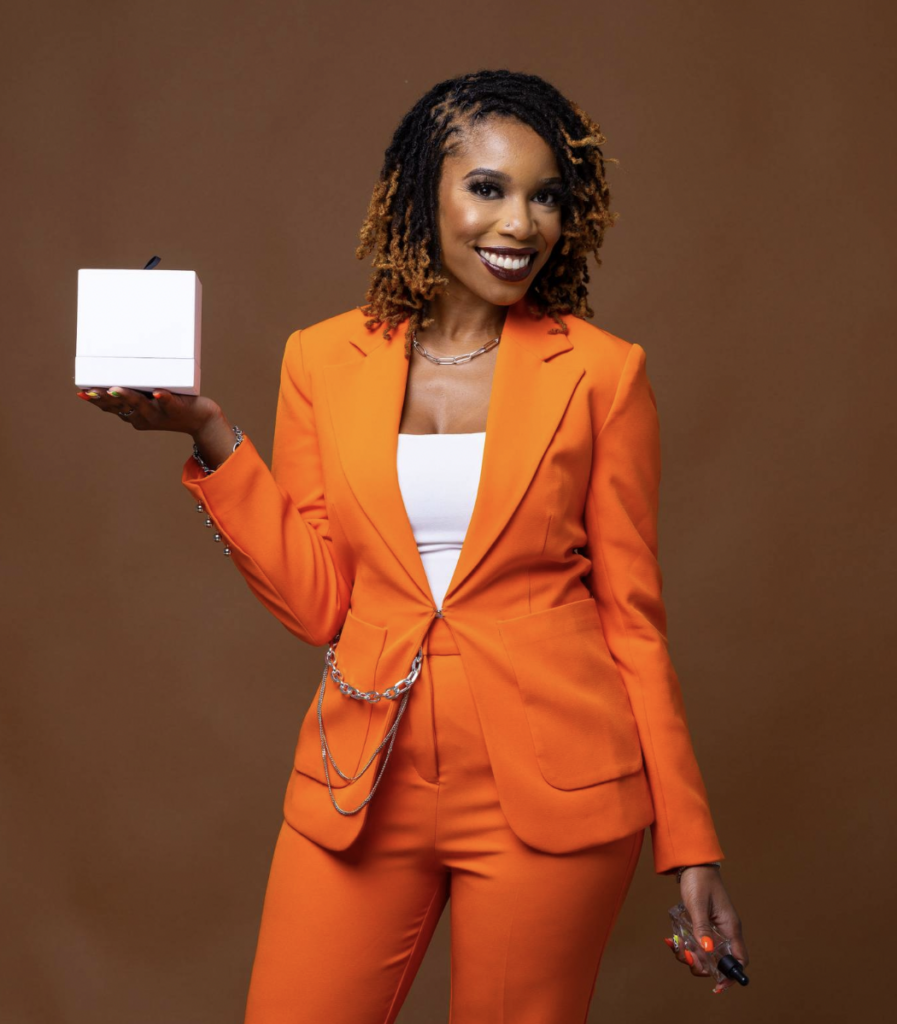
Megan Young Gamble, PMP® is a forward-thinking packaging and project management veteran with more than 10 years’ of experience transforming mere ideas into consumer product goods for today’s leading beauty, wellness, and personal care brands. Known amongst colleagues and clients for her perseverance and “see it through” mentality, Megan The Project ExecutionHER® is the owner and principal consultant of GLC, packaging & project execution team for CPG brands, Co-Owner of Pallet Pros, and Host of Product & Packaging Powerhouse Podcast.
- [FREEBIE] Learn about “day in the life” of a Packaging Project Manager → Get our “Starter Packaging PM Freebie” [link] https://glc.ck.page/thestarterpackagingprojectmanager
- Subscribe & Access our Video Vault YouTube Channel [ link] https://bit.ly/GLConYouTube
- Join our Email List [link] https://glc.ck.page/55128ae04b
- Follow and Connect with Megan on LinkedIn [link] https://linkedin.com/in/megangamble
- Learn about GLC, Packaging & Project execution firm for CPG brands http://www.getlevelconsulting.com
- Work with Me @ GLC, Schedule Discovery Call https://calendly.com/getlevelconsulting/15-minute-insight-session